In the fast-paced world of industrial storage, staying ahead of the curve is crucial. As businesses, big and small, strive to enhance productivity, efficiency, and sustainability, more companies are turning to innovative technologies to revolutionise how their warehouses operate. These technologies not only improve efficiency and productivity but also have a positive impact on the environment. For instance, implementing space-optimising automation and racking can minimise carbon footprints whilst simultaneously maximising storage density.
From Automated Storage and Retrieval Systems to warehouse space optimisation and data-driven software, the future of industrial storage equipment is here – and it’s changing the landscape of warehouse operation.
Automated Storage and Retrieval systems (AS/RS): Pioneering the way
Automation itself isn’t new. Most companies already incorporate automated systems to some degree. However, advancements in automation technology are accelerating at an increasingly rapid rate, with some forecasting that the future of warehouse activity will depend on the varied and extensive equipment automation can offer.
AS/RS can consist of shuttles, Autonomous Mobile Robots (AMRs), horizontal and vertical carousels, cranes and aisles, Vertical Lift Modules (VLMs), unit-, micro- and mini-load stockers, and many other systems which improve efficiency and accuracy. Powered by computer-controlled equipment, they eliminate and reduce the need for manual intervention. In turn, this helps reduce human error whilst significantly improving the efficiency and optimisation of storage space.
Autonomous vehicles and robotic technologies: Revolutionising product handling
The natural introduction of robotic ‘workers’ and piece-picking arms is a much-talked-about development that could deliver an unprecedented level of efficiency in industrial storage. They can operate 24/7, 365 days a year, with near-perfect success rates and precision. They can also handle heavy loads, minimise the risk of errors in inventory management, and relocate human resources to more value-added activities.
Machine learning algorithms power AVs, which can pick and place products efficiently, reducing the need for intervention. A robotic workplace also reduces repetitive, physically demanding tasks for workers, creating safer spaces and increased satisfaction. This shift in roles can contribute positively to workplace retention, fostering a sense of optimism about the future of work in the industry.
At the same time, Autonomous Vehicles such as Autonomous Mobile Robots (AMRs) and Automated Guided Vehicles (AGVs) are reshaping product handling within storage warehouses. Equipped with intelligent navigation systems and progressive sensors, they can quickly move around and integrate directly with data systems, ASRS’, the supply chain, and workers, creating a seamless workplace ecosystem.
Optimising space: Smart racking and high-density storage systems
Wasted space has long been a critical concern for storage companies, with up to 50% of warehouse space left unused due to poorly planned fit-outs or clunky workarounds. Innovative high-density vertical racking systems are now being installed in warehouses to effectively use the full height of the building, allowing items to be stacked closer together and increasing the volume of items that can be stored within the same footprint. While these systems can be a significant investment, the long-term cost savings from increased storage capacity and efficiency can often outweigh the initial costs.
Enhanced efficiency with AI
AI will be pivotal to the future of industrial storage, as it offers endless solutions to warehouse operations across various applications. AI systems can consistently analyse data and patterns and provide recommended process improvements. This can support better-optimised fulfilment processes, intelligent decision-making and seamless integration. AI can even predict which products are fast-moving and best placed in more accessible areas versus slower-moving items stored in less accessible areas.
AR and VR
Augmented Reality (AR) and Virtual Reality (VR) technologies offer many benefits in the industrial storage equipment space, revolutionising storage processes and warehouse operations. AR can improve navigation by delivering real-time information and guidance to workers, helping them locate shelves more efficiently. AR can also overlay details onto the product area for reduced search time and enhanced productivity. AR can also assist with maintenance tasks, such as providing instructional information, which can allow inspections to take place with more precision.
VR simulations can also provide more creative usage of tech in warehouse environments. By using them to replicate the layouts of warehouses and storage equipment locations, companies can enable workers to familiarise themselves with floor plans without overcrowding and risking employee safety. This can significantly improve the enrolment process for new starters and reduce the learning curve and risk of errors during employee training phases. However, it’s important to note that these technologies may require additional training or upskilling for workers to operate them effectively.
Innovative technologies will undoubtedly influence the future of industrial storage equipment focused on enhancing efficiencies, improving productivity, and delivering significant cost savings. The indisputable benefits of automation are also set to increase ROI, job satisfaction, inventory management, and accuracy and will revolutionise storage processes and operations. From AS/RS to AI-driven solutions, AR and VR technologies, and smart racking, embracing these technological trends will allow businesses to stay ahead of the curve and remain competitive and efficient, fostering a sense of hope about the financial benefits of these trends.
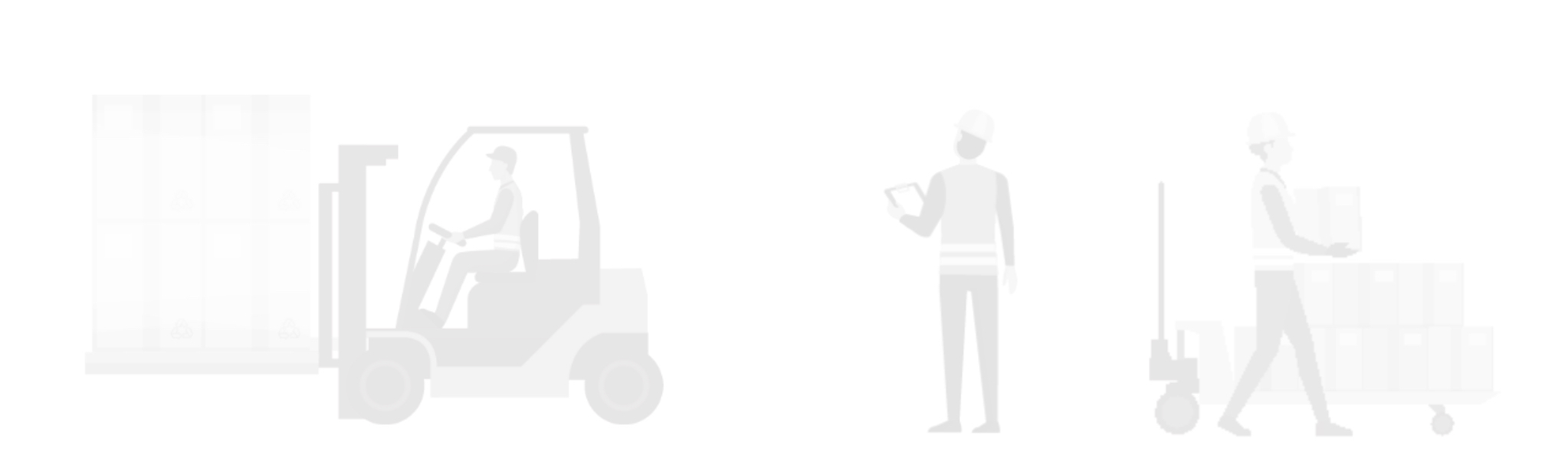
UK Market Leading Solutions
West Pennine Storage Equipment are proud to be a Tier One design and installation partner for Link 51 and Apex Linvar. Our relationship with Link 51 and Apex allows us to design, deliver and install the highest quality, UK-manufactured racking at competitive prices. As we are a highly recognised distributor of all storage facilities, we are also able to supply all other major brands of Pallet Racking, Industrial Shelving and other Storage Systems.
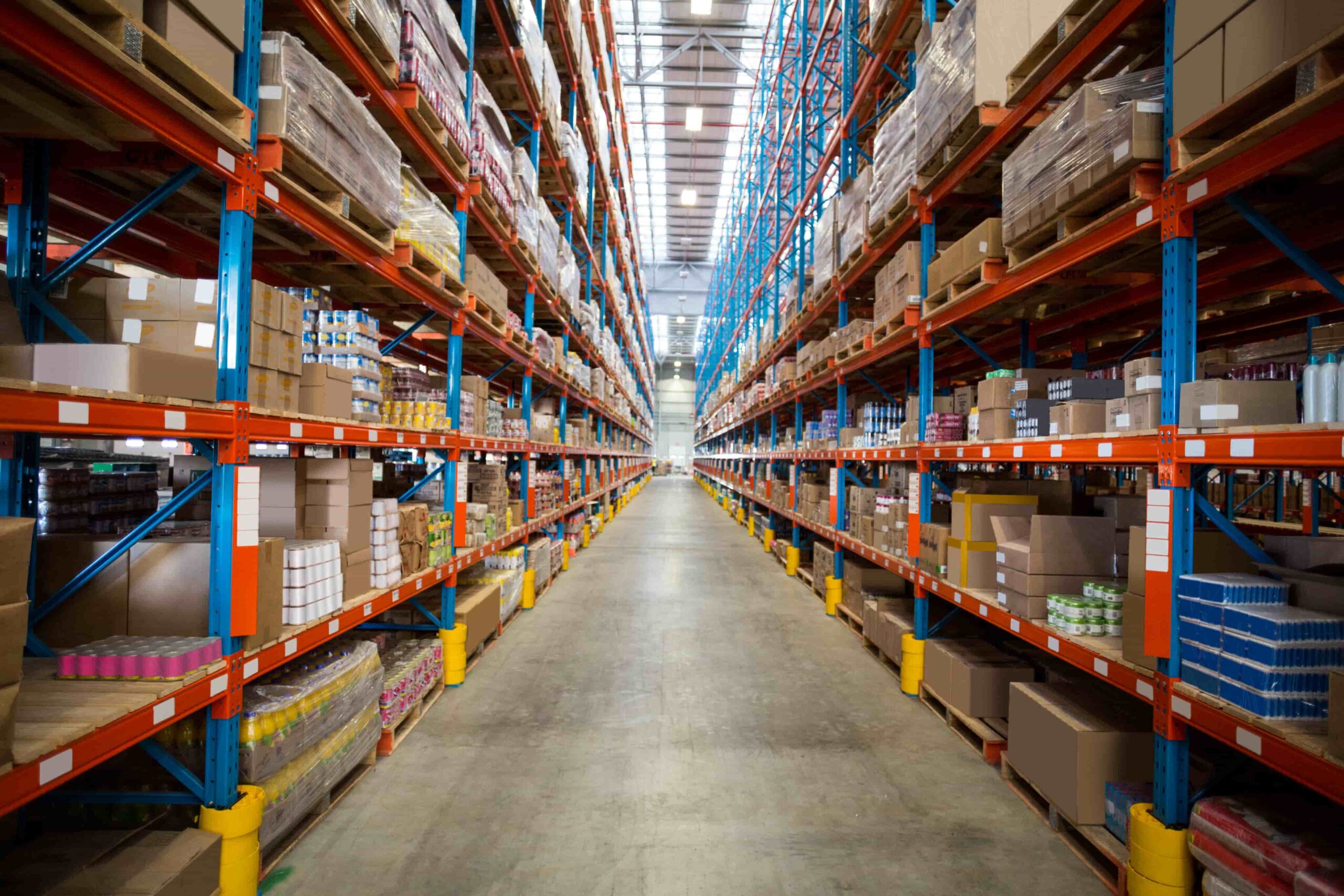